The Challenge
Over the next decade, 22% of skilled manufacturing workers will retire, and the industry is projected to fall a startling two million workers short of its need.
As a small business, Wyoming Machine found it difficult to recruit and compete for the talent they needed, such as welders, laser operators, and press brake operators. In addition to facing a technical skills gap, the company realized that a number of current and potential employees lacked basic math and blueprint reading skills.
- 2 millionworkers short of demand
The Solution
Wyoming Machine, Inc. is changing the perception of manufacturing careers, raising awareness about the opportunities in the industry, and providing training for employees through community partnerships.
To recruit and upskill future manufacturing talent, Wyoming Machine partners with other manufacturing companies and a local technical college to provide onsite, customized training to employees, giving them access to college credit courses through an interactive television system.
Changing Public Perception
Wyoming Machine recognized the immense need to change the outdated and unattractive public perception of manufacturing as a dark, dangerous, and dirty profession. The only way to do this was through community engagement.
The company began hosting and participating in:
- Manufacturing tours, which allows individuals to experience a modern-day manufacturing environment first hand.
- Gold Collar Career Day, an opportunity for high school students to visit Pine Technical and Community College (PTCC) to learn about careers in manufacturing.
- Women in Technology, a program introducing 6th grade girls to careers in STEM.
- Career fairs, specifically targeting unemployed and underemployed communities to promote career opportunities in manufacturing.
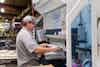
Community Partnerships
About 20 years ago, Wyoming Machine began partnering with other local manufacturers and with Pine Technical and Community College (PTCC) to discuss the future of the manufacturing workforce and address the growing shortage of skilled manufacturing talent.
In 2008, PTCC applied for and was awarded a grant by the U.S. Department of Labor to train workers for careers in advanced manufacturing. As part of the grant, Wyoming Machine was one of five partners selected by PTCC to receive distance eliminating learning equipment, which allows a PTCC professor to simultaneously teach in several locations at one time via video conferencing.
Wyoming Machine and the other manufacturing partners provided PTCC with input about the type of education and training that would be helpful, and today these companies offer on-site, customized training to their employees, giving them access to college credit courses while on the job.
While the original grant paid for the equipment and for the development of specific course offerings based on input from manufacturers, the manufacturing partners continue to cost-share to develop additional in-demand courses for their employees.
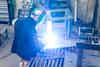
Breaking Down Barriers
Wyoming Machine’s partnership with other manufacturers and their local technical college allowed them to hire people based on their desirable qualities rather than direct manufacturing qualifications.
Despite being a relatively small business in a rural community, Wyoming Machine has successfully recruited skilled talent and continues to upskill their workforce to meet the changing needs of their industry. Their model for success is repeatable, and especially beneficial to employers in rural communities.